COST OF OWNERSHIP – CAN WASHER AND DRYER
Joe Bohlen, VP of Two-Piece Can Technology at Cincinnati Industrial Machinery discuss the facts and myths involved with the calculation of can washer costs.
Developing sustainable, low carbon, resource-efficient can manufacturing equipment with a minimum environmental impact is being monitored closely and will be of more concern for equipment and can manufacturers soon. More and more manufacturers claim that their machines are the most efficient with the lowest cost of ownership, but what is their frame of reference when making such claims?
Determining the total cost of ownership for equipment in a can plant is not necessarily straightforward and depends greatly on the complexity of the equipment.
If we exclude the amortization and the cost of the wear parts, the cost of ownership becomes the cost to operate. In a can plant, examples of the cost to operate vary from simple to complex. For a simple conveyor, the cost to operate is the power consumption of a few small electric motors. Add to this some wear parts and you have the cost of ownership.
A more complicated example would be a curing oven. Start with some large, medium, and small electric motors, add in the fuel for the burners, a bit of compressed air, and possibly a portion of the cost for a thermal oxidizer, and you have the cost to operate.
In a two-piece can plant, the washer/dryer has the largest amount of direct and indirect utility and raw material inputs. The pie chart below shows these inputs as a percentage of the cost to operate.
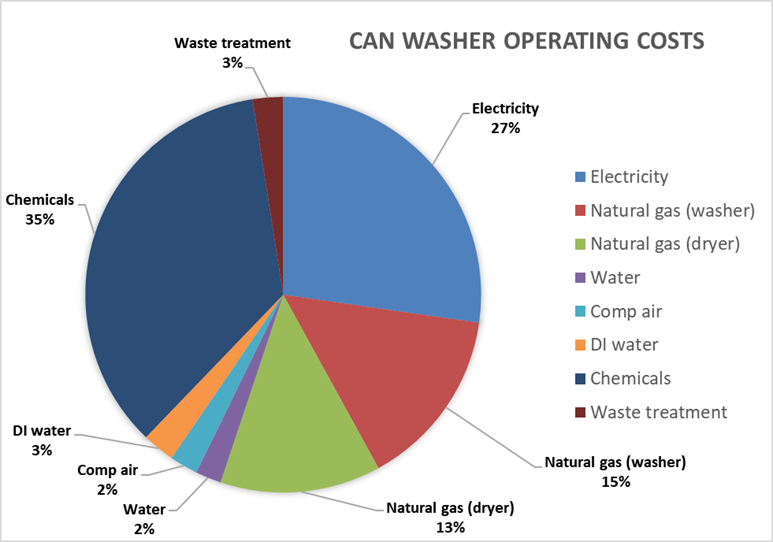
The indicated costs vary from the washer to washer based on the washer itself, its age, its maintenance history as well as the cost of the utilities from region to region.
Water cost is an input that can vary widely from one region to another. In our analysis, we use a water cost of USD 1.30/1000 gallons. In certain parts of the world such as the Middle East, water can be much more expensive.
Water also has a certain geopolitical aspect. Water conservation and sustainability are becoming major goals for can makers and much time, effort, and expense are being focused to reduce water consumption. Even if the water itself is not particularly expensive, the wastewater can become expensive to discharge if allowed at all.
The two other high percentage costs shown on the pie chart above are electricity and fuel. For our discussion, we use an electricity cost of USD .128/Kw-hr, and for fuels, we use USD 9.67million Btu as natural gas. The electrical power cost does vary worldwide, but not usually dramatically. The fuel cost on the other hand can vary quite a bit if the fuel is delivered to the plant in a liquefied form versus piped-in natural gas from a utility company.
Raw costs for a can washer can be identified on a cost per unit of measure, but there is a certain difficulty in measuring the effect of the interactions of various can washer features and functions.
The chart below shows the features and interactions that affect the consumption of utilities and chemicals.
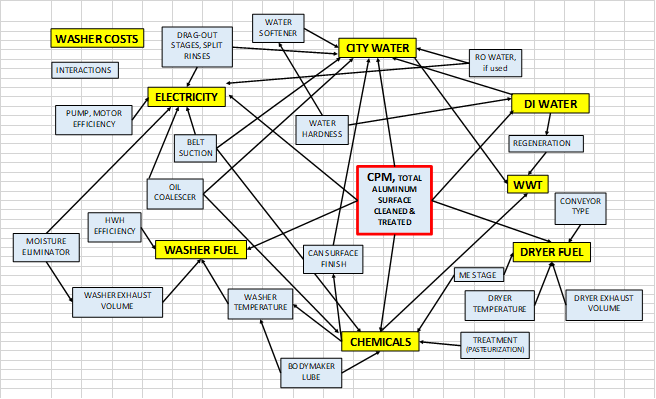
Here is a breakdown of the costs (shown above in yellow) and potential savings:
Electricity: The electricity cost is driven by the power consumption of the electric motors on the machine. Have your pumps been selected at the most efficient operating point to allow for the smallest motor possible? Non-optimized pump/motor combinations lead to excessive costs. Premium efficiency electric motors, direct-drive fans, and variable frequency drive further help to reduce power consumption when the full flow of the pumps or blowers is not required.
Some of the interactions involved with power consumption are oil coalescer, belt suction devices, split rinses, and drag outs with multiple small pumps. All these features require more power, but they normally pay back with chemical savings and water reduction goals.
City water: How good is your incoming water quality? Does the hardness of the water lower the cleaning and rinsing ability of the washer? Does the hardness reduce the efficiency of your DI system? Would the investment in a water softener reduce the overall volume of water consumed? In certain situations, with incoming water, pre-treating the water is the best way to reduce overall water consumption. As far as overall washer water consumption, the optimum water backflow system is one where water flow is controlled in response to can throughput. This enhanced function puts water consumption in proportion to the metal surface being processed and in modern can washers, gravity backflow further reduces the electrical usage.
DI water: Is water de-ionization the best way to do a final rinse of the can? Will your customer base allow you to switch to RO water? There is an electrical power cost to RO, but the reduction of effluents from resin column regeneration can help with overall water reduction. The permeate/reject split from an RO system can be used in some innovative ways on a washer to reduce overall water consumption.
Wastewater Treatment (WWT): Any reduction in chemical or water use will lower the volumes through the wastewater treatment system.
Dryer Fuel: Dryer fuel consumption is mostly a function of operating temperature, the water that is evaporated, and the exhaust rate. These three factors account for about 70% of the heat load for a can dryer.
There has been much discussion and several claims made about the thickness and construction of the insulated walls of dryers lately. Regardless of construction, less than 5% of the energy used in a dryer escape through the walls. Reducing through wall heat loss is certainly worthwhile, but it is not the greatest energy-saving improvement that can be found.
Another false economy claim is noted when someone says: “I put a more efficient burner on my dryer”.
In the case of a can dryer where the burner heats the air directly, and where fresh air being pulled into the dryer is normal and desired, all burners that are performing combustion properly are 100% efficient. If the burner is not burning dirty, 100% of the fuel you are purchasing is being converted to heat for the dryer. A case for a high-efficiency burner is where an optimum flue gas temperature is desired such as in a boiler or similar heat exchanger system.
Dryer energy savings come from:
Reduce the water: The use of ME provides a better water break on the surface of the can and therefore reduces the water volume dragged into the dryer.
Reduce the exhaust rate: Excessive exhaust does indeed reduce the dryer humidity to the very lowest level, but there is a point of diminishing returns where drying is not improved by more exhaust. A VFD on the exhaust fan can help find this optimum point of exhaust volume versus humidity.
Reduce the dryer’s operating temperature: Unlike a curing oven, a dryer just must get the last bit of moisture out of the can. Selecting a single operating temperature to just barely dry the cans in all conditions is difficult to do. There are a few semi-automatic ways to let the machine’s PLC select the best temperature operating point based on the washer operation and throughput.
Switch to a Kevlar mat: A metal conveyor belt absorbs and carries out up to 20% of the dryer’s heat, and the use of a Kevlar belt cuts this heat loss by more than half.
Chemicals: The chemical costs for a washer can vary with several factors. Is your tank make-up water particularly hard? Are you using a treatment (Stage #4) chemical? What sort of surface condition do you need out of the wash stage? Does your body maker coolant present any unusual cleaning problems? Can you switch away from the fluorides found in most washer chemicals? Any reduction in chemical consumption will also drive reductions in water and WWT costs.
Washer Fuel: As washers are generally hot water or steam heated, the fuel efficiency starts with the efficiency of the water heater or steam boiler. Heat consumption of the washer depends on several factors and is driven by tank operating temperatures. When the chemical system is set up properly, the operating temperature can be set at the chemical supplier’s minimum recommended level. If cleaning or can surface problems show up, the first step should not be to raise the tank temperature. Checking the chemical setup, the spray pressures, the spray pattern, and clogged nozzles should be the first items to check. Additionally, washer housing exhaust is the main source of heat loss, so the lower the operating temperature, the lower the energy consumption. The washer exhaust is set to provide good housekeeping around the washer by catching escaping steam. The excessive exhaust will raise the heat load considerably.
When the interactions within a can washer/dryer can be identified, the machine costs can be better understood. Once these costs are understood, improvements and cost reductions can be effectively made. Based on our outlined approach above, we believe that a 2400 CPM washer/dryer, built with some of the most common options will process cans with an operating cost of about USD .75/1000 cans.
We would be curious to hear from you to see how this figure might match your experience.