The recent growth of the beverage can business in the US and around the world is well known.
Aluminum cans are displacing other forms of beverage packaging, and the recent uptick in grocery store sales (vs. restaurants) due to the pandemic has also boosted the growth of beverage cans.
The beverage can business is not the only can business to benefit from increased grocery store buying caused by the pandemic, food can sales are also significantly up.
For example, Campbell Soup expects people to continue eating more at home even after the pandemic ends. The pandemic has provided food makers with an unprecedented opportunity for millions of people to try their products for the first time in years.
Steel food cans are made in a similar way as aluminum beverage cans, but there are some notable differences in the manufacturing process.
The can material is tin-plated steel and formed in the same way as aluminum cans with an uncoiler, cupper, body maker, and trimmer.
Following the forming of a trimmed can, the other steps of the steel food can-making process are dramatically different. The can is not normally decorated as it generally gets a paper label, and the sidewall is often beaded to resist vacuum packing. The dome is also different, again for purpose of vacuum packing. The can is flanged, but not normally necked.
From the point of view of the can washer and dryer, the process is also much different than aluminum can processing in its industrial machinery.
The lube used in the body maker for steel cans is somewhat different than what is used for aluminum, and this lube is easier to remove in the industrial washer.
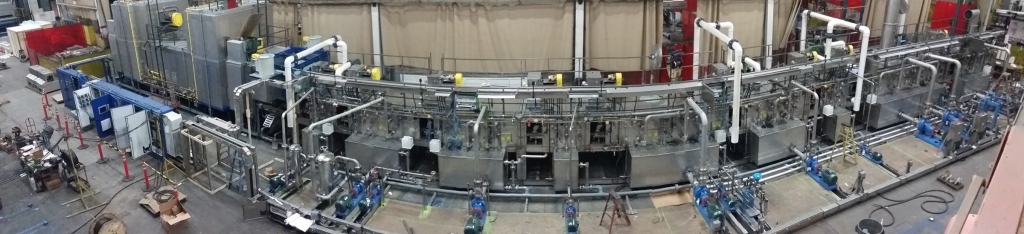
The washing chemistry in a food can washer is much more benign. There are no strong acids or fluorides involved in the can washing. The chemistry is much less corrosive to the industrial washers and waste treatment is much easier to do.
Additionally, there is no chemical treatment stage and no mobility enhancer stage used for steel food cans. Washing steel food cans is just removing the oils and then rinse.
What is different about steel cans is that in most cases, the product that is packed in these cans must be heated in some way. That is, a retort or pasteurization process often follows the food packing.
To minimize any rust staining in the wet post-packing heating, an exterior coating is applied to the cans after washing.
The external coatings that are commonly used are epoxies or acrylics, depending on what the post packing heating process is, and are applied in mass by way of waterfall curtains between the can washer and the curing ovens.
The challenge with applying this coating is that the cans must be kept separated to minimize contact marks and voids on the coating as they pass under the curtains. Specially designed magnets in the can transfers are used to maintain the properly shaped pack as the cans travel through the machine. Viscosity control of the wash cost material is also important to maintain a consistent film thickness.
After wash coating, the cans go through a “semi-cure” in an oven. The cans are dried to the point where the exterior coating is tack-free. At that point, the can inside is sprayed and then the final full cure of the external coating takes place in the inside the bake oven.
Beverage cans may be getting most of the headlines these days, but the food can business has a growth story of its own.